Sourced from New Zealand Truck & Driver – 25 Jul 2023
https://pressreader.com/article/281964612324828
The job. While they might be on the same run each day, the actual routes and premises visited are different every day of the week. One customer might want a bin emptying every day but 50% of the customers might be different on the second day, and the next, as Rubbish Direct picks up rubbish as and when each customer wants.
“So when the customer says jump and we say how high and they say we only want our rubbish picked up after 10am, we say no problem – but our competitors are going to struggle to get to that level of granularity.”
In a day, trucks in the central city often do two sweeps to hit the right time frames making, typically, 80 stops and emptying 400 bins in an area that might be only 2km across. Drivers have a tablet setting out each run’s route each day with any new or special requests highlighted.
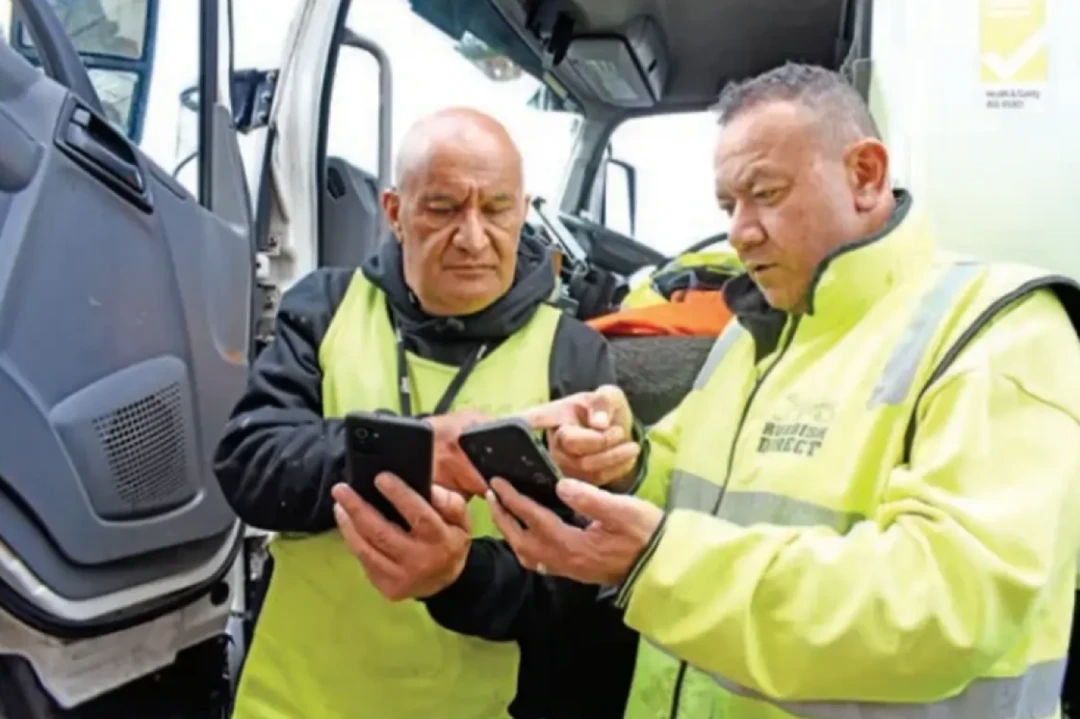
I’d assumed tools like Google Maps would be useful for route planning but no – Rubbish Direct’s workflow software has been designed in-house by contract developers. One of the key reasons is that they only want trucks turning left and collecting on the left. They only turn right at traffic lights.
Even then, congestion and roadworks often mean the planned and actual routes can vary, and there is constant interaction to streamline and update the process. “We are always going why did that happen, and why did that happen?” says Mark.
Mark says growth in the business has been relatively steady since day one. He says if growth slowed it would be a sign he was doing something wrong. Even when he has had to put up prices – the cost of landfill rose a hefty $20 a tonne this month – he got just two customers pushing back out of two thousand. Mark says even when communicating price rises, he gets more messages of support than complaints.
Mark arrived here from England in 1993 – his mother was a Kiwi – and got into selling cell phones. He was a manager at Telecom when he decided to help out a friend who wanted to start a business, actually buying the friend his first compactor rubbish truck in 1999. They worked together building the business until 2015 when Mark became sole owner.
The turning point that set the direction for the company came when they won a contract for the Hyatt hotel. It wanted glass recycling collected quietly, which meant not tipping bins into the back of a compactor truck. They bought an Isuzu boxbody truck with a tail lift to collect bins and replace them with empty ones.
It set up a model they used successfully for a host of hospitality clients in Auckland’s CBD until that business ground to a sudden halt during Covid. It wasn’t as bad for Rubbish Direct as it was for the bars and restaurants ordered to close but overnight it lost 40% of its business. Mark says they managed to retain staff using subsidies, annual leave and shorter hours but they also restlessly looked at reshaping the business.
The bar and restaurant businesses, which produce a lot of glass, are coming back, but since Covid, Rubbish Direct has found it can still collect most of this with compactor trucks, reducing the need for box bodies.
“What we have found largely is that the apartment recycling helps cushion the glass. We get a lot of cardboard, plastic and milk bottles from them and we don’t overcompact the stuff, so it retains the integrity of the glass. We were actually quite surprised. So it changed how we operate quite significantly.
“Where we still have customers that have large volume of glass only we’ll go and pick all that up in a box body truck.
“We’ve actually got just the two models,” Mark says. “There’s the NPR which is the boxbody and there’s the FSR which is the compactor. They are all Isuzus. You look at them all and within a little bit they all look exactly the same.”
Having one truck throughout the fleet simplifies maintenance.
“If we’ve got one type of truck it’s easy to have a spare engine on the shelf and spare gearbox on the shelf. We can have spares for whatever it is because we’ve only got one truck to have spares for.”
Mark says they don’t have a replacement strategy yet and he is just beginning to wonder when the right time to replace the older trucks in the fleet will be.
“I’ve just got rid of the first trucks I started with which were 1994 import Isuzus. We started buying brand new vehicles in 2005.
“The oldest compactor that we’ve got now is 2008, so that’s 15 years old and still going strong. We repaint them, we reline the body and bowl. So I’m still figuring out what makes sense. Of course the cost of new ones is going up and they will only do the same work.
“Maintenance hasn’t really ramped up. We do really low kilometres but lots of hours. A truck might only do 100 kays in a day but it will do 10 hours of engine time just running the PTO. I don’t know if it’s an Isuzu reliability thing, but we don’t seem to have any issues with engine wear or that sort of thing on those new vehicles.”
The trucks also run fairly light at no more than 11 tonnes. “We’ve only had one that’s been a problem. The turbo had an issue and it started running on sump oil and the engine ran away with itself. We couldn’t stop the damn thing and it just ran flat out until it ran out of sump oil! Of course, now I know you can pull the air filter off and stuff a rag in there and choke it – but we didn’t even get it reconditioned. It ran for another 170,000km before it finally gave up,” he laughs.
“That was what prompted me – I thought I’d better get a spare engine in case that happens again and to date we’ve never used it.
“I guess that what diesel engines are really good at – 1200 to 1500 rpm is enough torque to keep the PTO going but it certainly doesn’t seem to stress the motor. They seem to go really well, so I’m guessing the thing that will start to nail them will be rust but we’ve got an engineer that does all our bodywork, rust, so, at the moment, fingers crossed it’s all going good.
“I guess because we’re doing the maintenance on our own trucks we probably look after them a little bit better but certainly you know, a vehicle at 15 years old is still what we would call a good vehicle.”
Rubbish Direct employs its own mechanics, doing all the work in-house, even to the extent of having its own roller brake test machine installed on the floor in the workshop bay.
Mark has always bought Isuzu vehicles, getting a Fuji.
Heavy Industries compactor installed in Japan, a combination he said was, and still is, vastly superior to other models available here. He now buys the combination from local agents Robertson Isuzu in Palmerston North. Envirowaste and Waste Management have followed suit and are also buying them from Robertsons.
Externally, the trucks have changed very little over time which helps Mark maintain the fleet’s consistent appearance.
“We’ve had minor upgrades in the truck which is really around emissions control and that sort of thing – we’ve gone from Euro 3 to Euro 5. We’ve had things like DPFS come in, but really very little has changed.”
Mark did consider other vehicles at one point and checked some out. “I took one for a drive and I thought oh yeah it doesn’t have power mirrors and it doesn’t have an air thingy seat in it so the guys aren’t going to be as pleased driving that as they are with what they’ve got now. It just didn’t seem to be as nicely specced. I mean our guys spend 10 hours a day in those trucks and I would like for them to be as comfortable and luxurious as possible because that’s their office, and if I was doing that I’d want to have a nice office.”
Mark would prefer to give each driver his or her own truck but the trucks work seven days while the drivers only do four or five. He is keen for the drivers to keep them clean inside out of respect for their colleagues and their customers and if an issue is raised he will have a word. He is very keen that everyone lives the company values, one of which says everybody is in the marketing department “and that includes our trucks and bins” says Mark, with a laugh.
Sourced from New Zealand Truck & Driver – 25 Jul 2023
https://pressreader.com/article/281964612324828
Peace of mind with job security and a stable employer with family values.
If you have the right to work in New Zealand, a Class 2 truck licence, know what work ethic and values are, and believe that the harder you work the luckier you get then read on.
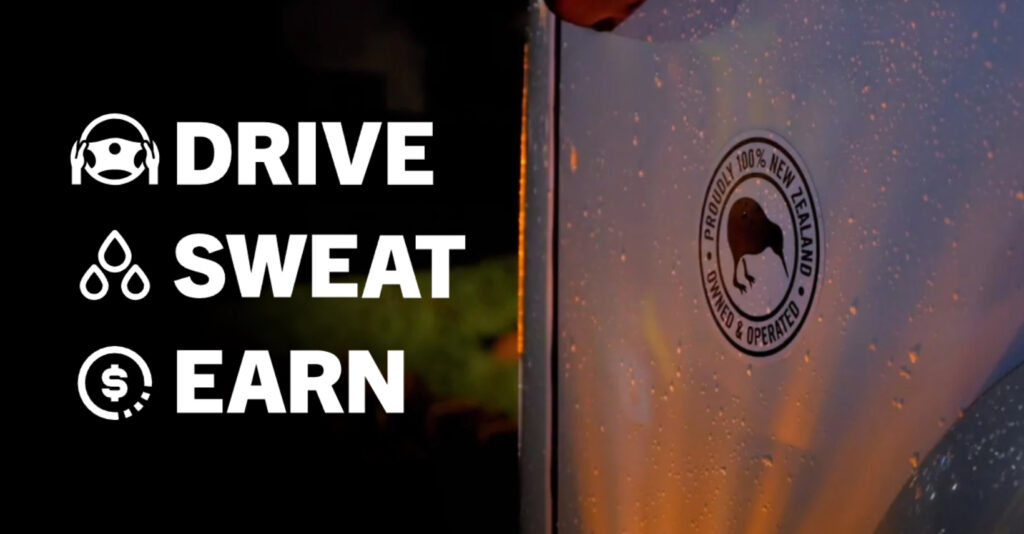
We have opportunities for people who want to keep fit, or even people who want to get fit, to join our team collecting recycling and rubbish in the Auckland region.